
CNC turning and milling – what’s the difference?
by Karen Friendship, Managing Director.
Turning and milling, at first glance, appear to be very similar processes and achieve similar results. So, what is the difference – and why do we offer both processes? This was one of the things that confused me in the early days of my career at Aldermans. While many of our customers will already know the answer, others may find this a useful insight into what goes on behind the scenes in the world of metal fabrication!
CNC machining
Often turning and milling are generically referred to as “CNC machining” – our customers often ask for CNC machining rather than for turning or milling by name. Of course, it’s our job to make sure that the most appropriate process is used each time.
Put simply, the difference between the two processes comes down to which part moves – in general terms, the metal or the machine.
- With CNC turning a metal bar is fed into the lathe and rotates at speed while a single-point cutting tool removes portions of the metal to create the desired shape.
- With milling the metal usually remains still while multi-point cutting tools rotate around it.
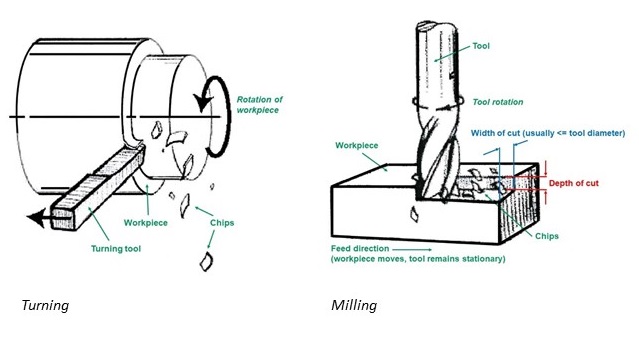
Turning
Items processed by a lathe will be cylindrical and must be on-centre. Turned parts can range from simple rings to complex curved components. CNC turning is the most efficient way to mass-produce these kinds of parts.
Various cutting tools can be installed within the lathe tooling head (pictured below) to perform different cutting operations sequentially, to produce parts in a one-pass process. Straight cuts, tapers and contours can all be created by varying the angle and depth of the cut.

These pictures below show a billet being turned on the lathe (fixed into the turret); and the finished result, where straight and tapered turning has been used.


Watch our video of CNC turning in action, below:
Milling
Milled parts are not necessarily cylindrical. Milling machines use multi-point cutting tools; and there can be more than one tool working on the piece at a time. Milling may be the preferred choice if the part needs anything which is off-centre or angled (such as holes or cuts), or for secondary features such as indentations or grooves.
Here are two pictures of milling in action, where the part is being drilled.
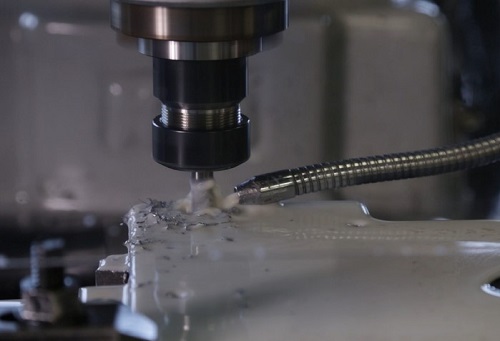
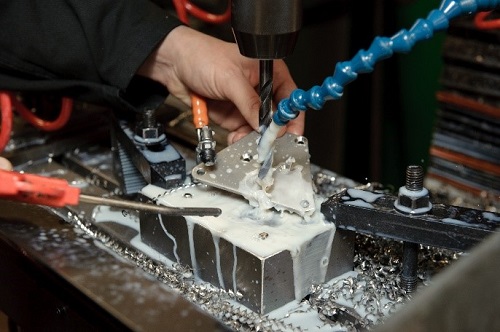
The milky-white fluid shown in the pictures is cutting fluid, which acts as a coolant and lubricant. At Aldermans we use a water-based emulsion in all our turning and milling processes.
Milling can be used to shave material from the surface of the workpiece using a tooling head with multiple cutters (plain milling or face milling); or to shape its edges using a cutting tool with a thread (profile milling or side milling) – examples shown below.


Our turning and milling service at Aldermans
For CNC turning work, we currently have two automatic bar-fed lathes which can be manually set or programmed to run unmanned. We offer manual milling at present – but CNC milling is part of our business development plan.
In terms of tolerances, generally we state within 0.01mm for milling and 0.025mm for turning – but our skilled toolmakers love a challenge and always aim to hit the mark precisely!
Because we have such a wide range of metal fabrication technologies here at Aldermans our quoting team always looks closely at what the customer requires to determine the most cost-effective approach. We sometimes have different ways of achieving the same result, and we look at the process dynamically as a job progresses, to reduce lead times through the factory. This is why we put such a strong emphasis on our lean skills and production planning techniques.
Contact our estimating team for a turning or milling quote, and for advice on the best metal fabrication process for your job.