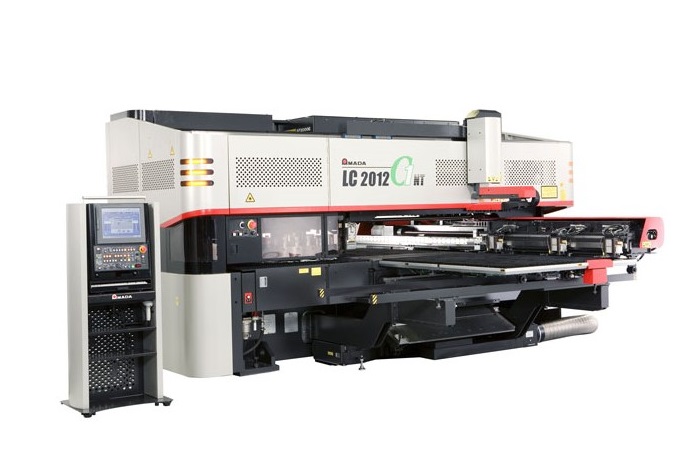
New automated Amada LC2012 C1 combination machine installed
Like everyone in the manufacturing sector, the recent recession proved to be a challenging trading period for Aldermans, a reputable company of some 40 years standing. However, a combination of determination and resolve saw the business through, and now, with improving economic conditions, Aldermans is implementing a new strategy that includes provision for ongoing investment in the latest manufacturing technologies.
Like everyone in the manufacturing sector, the recent recession proved to be a challenging trading period for Aldermans.
However, a combination of determination and resolve saw the business through, and now, with improving economic conditions, Aldermans (a reputable company of some 40 years standing) is implementing a new strategy that includes provision for ongoing investment in the latest manufacturing technologies.
While Aldermans supplies to all industries, the company identifies four sectors that are key to revenue growth: transport/automotive, specialist furniture, industrial, and retail. This diverse manufacturing company supplies components and assemblies ranging from airport terminal furniture and car parts, through to electrical enclosure components and point-of-sale shop fittings, to name but a few.
“After a tough recession the order book is now looking good and we are profitable once more, hence the decision to invest,” says the company’s operations manager, Rob Johns. “We have ambitions to become a national rather than regional player. At present, many of our customers are located within a 40 mile radius of Plymouth, but our investment programme will help address this issue.”
Aldermans was previously running two punch presses and a laser cutter.
While all had given first class service, in the words of Mr Johns, they had become a little ‘tired’. “To outperform the competition and make our new strategy become a reality we realised that new investment was the only way forward,” he says. “As part of a lean manufacturing project we decided to change our entire factory layout, clearing out redundant equipment and reducing our inventory to improve efficiency. Replacing two machines with one made perfect sense so we part-exchanged a punch press and laser cutter for an Amada LC2012 C1 punch-laser combination.”
Mr Johns says the ISO quality-accredited company shortlisted four different combination machines and selected two for time studies.
“Of the final two, we chose the LC2012 C1 not only because it is quick and competitive on cost, but as we had Amada machines previously we could vouch for the high level of service provision. Amada is renowned for its service and this kind of support is invaluable to a company such as ours.”
The LC-C1 punch/laser combination machine, nicknamed Cheryl, provides ultimate flexibility without compromise.
An energy saving single AC servo drive motor provides 20 tonnes of variable punching stroke, while both the nozzle and lens offer quick-change laser technology. Furthermore, a 49-station punching turret is provided to accommodate even the most demanding of jobs.
It’s no secret that punching is faster than laser cutting when it comes to the use of standard tooling to produce repeat features. For this reason, most manufacturers with combination machines punch as many features as possible to achieve better cost per part, while the laser is used for aesthetic profiling, or on apertures for which there is no tool.
Installed just before Christmas 2010, the Amada LC2012 C1 has already begun making real parts at this 40 strong family-owned and run business. Labour allocated to the previous non-automated machines was redeployed – no jobs were lost.
“We’re a single shift operation but the flexibility of the automated Amada combination machine effectively makes us a three-shift, 24-hour facility because we can run unmanned, lights-out,” explains Mr Johns. “Despite the reductions in cycle times and set-up times, and the improvement in accuracy, it’s the automation that provides us with the biggest benefits. In our business, quality and delivery are assumed – it is price that wins orders and the best way to drive prices down is through automation.”
The unmanned capability of the Amada LC2012 C1 is delivered thanks to an integrated part remover (PR-C1) for automatic picking and stacking of finished components. Additionally, Aldermans took an automatic load/unload system (MP-C1) to provide lights-out operation for sheet sizes up to 2500 x 1250 x 6mm (up to 3.3 tonnes of material can be accommodated).
Aldermans processes materials that include aluminium, mild steel and stainless steel.
Sheet thicknesses range from 0.9 up to 6.0mm, although 1.5-2.0mm is typical on a day-to-day basis. While batch sizes are usually around 50-100, prototypes are also common, and this is an area that will be boosted by the arrival of the LC2012 C1.
“The Amada combination machine will make the supply of prototypes much more cost effective than before thanks to its flexibility,” says Mr Johns. “As a company we openly seek quick-turnaround prototype work. In our experience, the supplier that makes the best job of prototypes is often rewarded with the production contract. Over the years we have nurtured a strong prototype arm to our business and today we are able to quickly transform customer ideas and concepts into value engineered products, from single prototypes to volume Kanban parts.”
There is no doubting the lift that the arrival of the new machine has given to this £4 million turnover company.
“The workforce was very buoyant when the investment was announced.
“Having now seen it first hand, everyone is convinced the company is looking forward to a prosperous future. It’s been a real confidence booster and the machine has already started earning its corn. One new job we picked up last year has now been transferred to the LC2012 C1. Previously we broke even on this job, now we make a profit.”
To underpin company growth, Mr Johns says the plan for the future is further investment – possibly in 6-12 months’ time.
“While we have plenty of direct competitors, few have punch-laser combination technology, and fewer still have a combination machine that is so well specified in terms of automation,” says Mr Johns. “We see it as a real differentiator and hopefully, so will our customers.”